Technical Analysis
The launch of the Alpha Tauri AT01 marked the beginning of a new era for the former Scuderia Toro Rosso team. But despite the new team name, chassis name and new livery, the AT01 is an evolution of last year’s car.
‘The biggest opportunity this year has come from continuity [of the regulations] so we have had the opportunity to evolve the car is some areas,’ says Jody Egginton, Technical Director of Alpha Tauri. ‘There have been numerous changes [to the 2020 rules] but nothing that’s suddenly ignited a huge development stream. It’s taking everything forward and doing what we do every year really which is revisiting [everything] with a set of regulations which haven’t evolved massively.’
The AT01 runs the Honda RA620H power unit and similar to previous years, also features Red Bull’s 2019 gearbox. With the inboard suspension integral to the gearbox, these components are also carried over as well as the majority of the outboard suspension.
‘There’s certain areas where we can push harder, so we’re very focused on further optimising the power unit packaging, really trying to shrink wrap the body work,’ highlights Egginton. ‘Other areas where we’ve focused on is improving the control of the upper and lower wheel wakes and how they work. Especially the upper tyre wake because that gives us opportunity to get better flow to the back of the car. We’re also doing the brake ducts ourselves as that has become a listed part.’
Nose
The general shape of the nose remains similar to last year’s STR14, however the S-duct has seen some modifications. Firstly, the profile of the NACA inlet ducts have been changed slightly, as highlighted below.
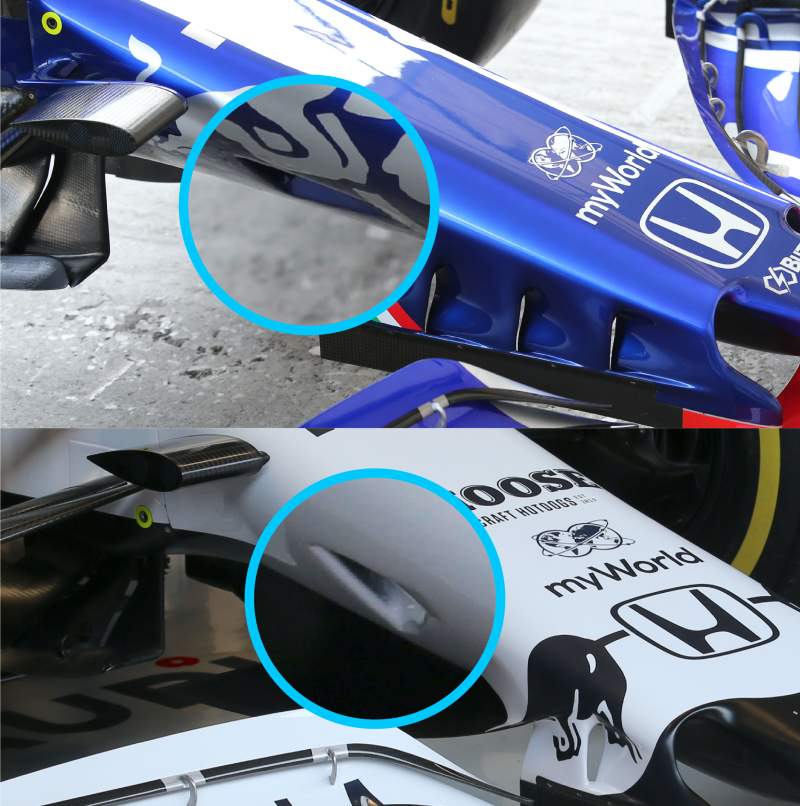
Secondly the outlet at the top of the nose is now much more Red Bull-esque with a pronounced outlet duct featuring a slit at the front. This slit could be some form of inlet which could help to suck more flow out of the S-duct, but this is speculation. ‘Everyone is running an S-duct of some description and we’ve refined it this year aesthetically,’ says Egginton. ‘It’s now more similar to Red Bull and a few other teams, but again it’s grabbing more performance from it and I guess with evolution comes convergence.’
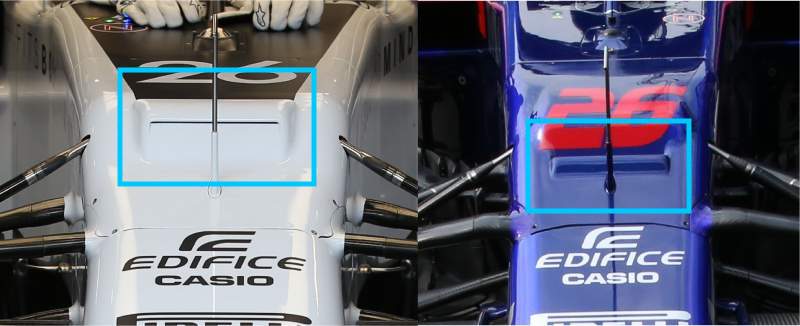
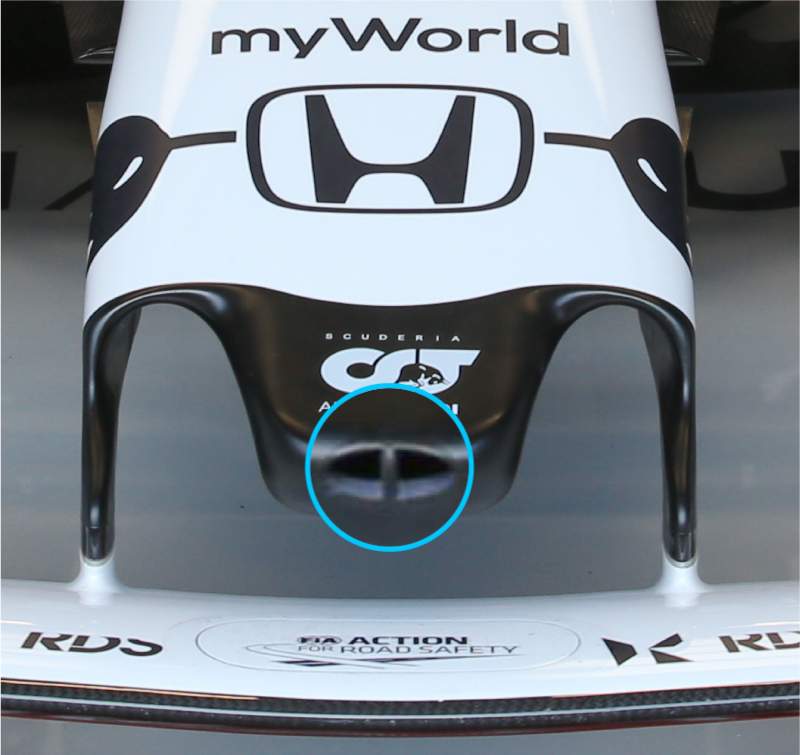
In addition to the NACA ducts located on the side of the nose, some teams also incorporate inlets on the very tip of the nose. These have two functions; 1) feed the S-duct 2) provide cockpit cooling.
‘For sure, some teams are using [the inlets] as an S-duct feed but in other instances it could just be something as boring as a feed into the cockpit as there are similar advantages in cockpit cooling,’ confirms Egginton. ‘There are a range of approaches, some cars run the inlets just inboard of the pillars, while other run the NACA ducts along the underside of the nose and some from the shroud. We had those last year for instance. So there are a range of places you can grab that air and throw it out a slot further along the nose structure.’
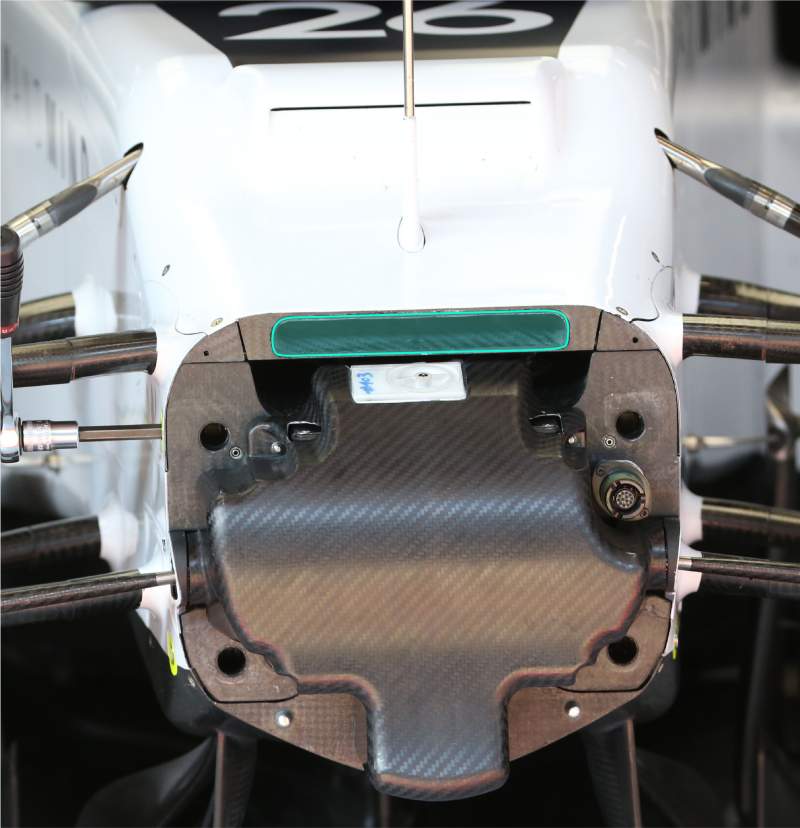
To displace the turbulent flow coming off the front wing into the cockpit, channels have to be incorporated into the nose. These can either be singular or twin channels, which the nose inlet and the S-duct inlets feed into. Here we can see that the AT01 features a single channel which feeds the S-duct S-duct outlet at the bridge of the nose.
Another development area for this year has been the devices which hang off the nose, including the ‘cape’ (highlighted in blue below) which works together with the front bargeboard area (highlighted in red below). Whereas, last year’s STR14 featured a smaller cape but a larger front bargeboard.
‘Basically, you’ve got the flow off the first wing and you’re grabbing that flow with what we’re calling the cape, which is a device underneath, and then the forward bargeboard,’ says Egginton. ‘You’re trying to manipulate that flow and move that in the direction you want. That’s interacting, in some respect, with the lower tyre wake as well, so [the flow] is picking that up and then you decide what you want to do with that [flow].’
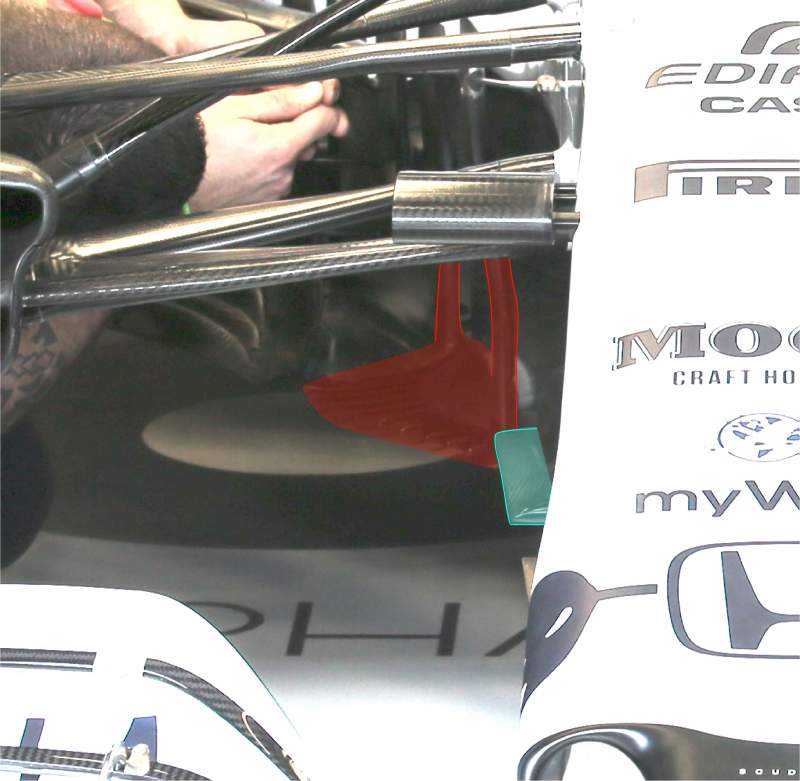
Of course, the aerodynamics package is not just optimised for straight, oncoming, clean airflow. Unsurprisingly, these areo devices are designed to cope with oncoming flows at all angles.
‘You also want to make use of that flow as the car yaws through the entire aero map and you might be more biased towards achieving a higher yaw characteristic for low speed performance. Our development is based on 6 or 10 metrics in the wind tunnel that we want to try and achieve,’ says Egginton. ‘It’s all to do with the subtleties of what you’re doing with those flow structures in the pillar area. It’s just that trade off between sealing the floor and getting the aero performance over the whole aero map really.’
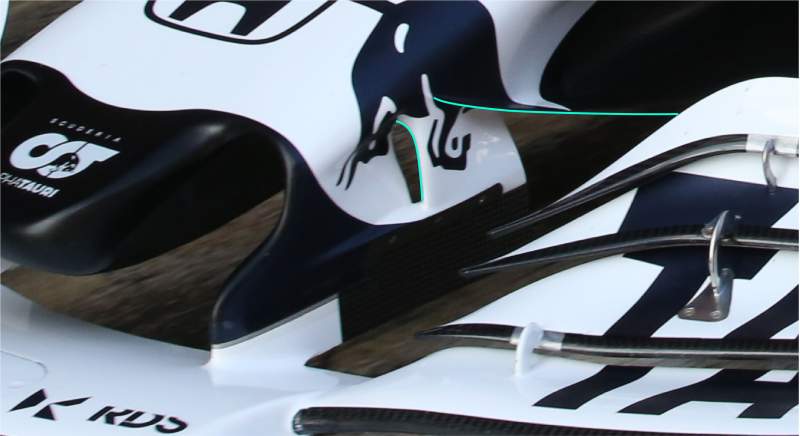